DEFINITION:
Quality is about meeting the need and expectations of customers.
As per ISO: Totality of features and characteristics of a product or service that bear on its ability to satisfy stated or implied needs is known as Quality.
There are many ways to define quality. Some of the most popular definitions for quality are listed below.
- Conformance to requirements
- Totality of characteristics which act to satisfy a need
- Fitness for use
- Fitness for purpose
- Freedom from defects
- Delighting customers
ASPECTS OF QUALITY:
Key aspects of quality for the customer include:
- Good Design- Looks and style
- Good functionality- it does the job well
- Reliable- acceptable level of breakdowns or failure
- Consistency
- serviceability
- Durable- it should last longer
- Good after sales service
- Value for money
IMPORTANCE OF QUALITY:
Good quality helps determine a firm’s success in several ways:
Accreditation to a recognized quality standard can also help you win new customers or enter new markets by giving prospects independent confirmation of your company’s ability to supply quality products.
Strong brand reputation for quality
Quality products make an important contribution to long-term revenue and profitability.
Quality is critical to satisfying the customers and retaining their loyalty.
The customers will continue to buy from you in the future if the product’s quality is good.
Retailers want to stock the product.
As the product is perceived to be better value for the money, it may command a premium price and will become more prices inelastic.
Fewer returns and replacements lead to reduced costs.
Attracting and retaining good staff.
The process of inspecting products to ensure that they meet the required quality standards”
- Quality control is the process of setting standards about how much variation is acceptable.
- The aim is to ensure that a product is manufactured, or a service is provided, to meet the specifications which ensure customer needs are meet.
- At its simplest, quality control is achieved through inspection. For example, in a manufacturing business, trained inspectors examine samples of work-in-progress and finished goods to ensure standards are being met.
- This method checks the quality of completed products for faults.
- Quality inspectors measure or test every product, sample from each batch, or random samples- as appropriate to the kind of product produced.
- The main objective of quality control is to ensure that the business is achieving the standards it sets for itself. In almost every business operation, it is not possible to achieve perfection. For example, there will always be some variation in terms of materials used, production skills applied, reliability of the finished product etc.
IMPORTANCE OF QUALITY CONTROL
- Higher profit and increased productivity
- Larger market share
- Quality Image.
- Customer’s loyalty
- Better utilization of economic and technical resources.
- Staff cooperation
- Reduction in costs
- Improvement in the Morale of employees – improve standards and produce quality goods
- Increase sales
- Customer’s satisfaction
ADVANTAGES
You have the time to adapt your planning and take decisions.DEFINITION:
With quality control, inspection is intended to prevent faulty products reaching the customer.
It pushes the factories to improve the quality level of their workmanship because of the pressure of inspections and non-acceptance.
You don’t discover any last-minute surprises or quality problems after the goods are delivered.
Inspection is measuring, examining, Testing & gauging one or more characteristics of a product or service, and comparing the results with specified requirements to determine whether it conforms.
- It maintains the product’s degree of excellence which results in higher sales/profits.
- As the supplier is aware of the 3rd party inspection for the respective order, they will work on maintaining the expected quality of the product from the beginning.
- It forces your suppliers to meet buyers order terms and product requirements. Otherwise, they may need to compensate buyers for any discrepancy against exact materials, colours, aspects, packing, functions… etc.
- Buyers will discover the quality problems at the supplier premises which will save time, energy, and cost of rework for them.
- Conducting a Final Random Inspection before a week or 10 days of shipment date will allow enough time for taking the final decision of the shipment.
- Over the long term, regular inspections will contribute to improving your supplier’s performance and reliability.
- Inspection cost is only 1-2% of the total FOB value of the goods at Stake.
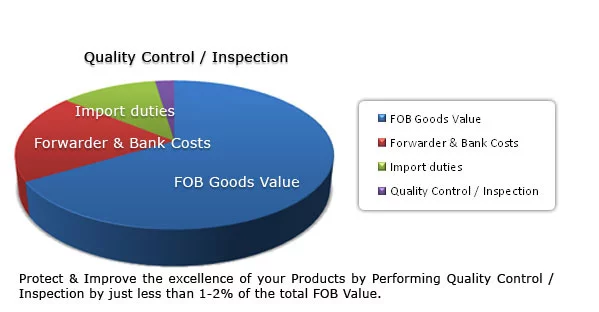
Buyers who do not do Quality control / Inspections have experienced these below Problems.
- The products are not sold due to too many visual defects such as holes, stains / Wrong size / Wrong price tag, etc. That affects the sales of the organization.
- Products made with cheaper materials than the approved quality. Those poor-quality products reached Import destination without sorting it in the supplier premises.
- Sourcing cost exceeds the budget as the buyer needs to sort our defective products and re-work them in the Importing country.
- Credibility of the brand is affected when Poor quality products are delivered to the customers. The Buyer’s brand name & image suffers because of Poor quality delivered to customers.
- Besides the brand image, the company’s sales and profit also decline due to loss of customers, higher product returns, and recalls.
FRI is an Onsite random inspection to verify if bulk meets approved quality / contract requirements. It helps to verify product’s Quantity, Visual quality consistency and Functional property.
FRI is also called as Pre-shipment Inspection (PSI) or Final Inspection.
This Inspection is normally conducted
- At on-site or source where product is manufactured and sometimes at forwarder’s premises.
- At the stage when 100% production is completed and at least 80% goods are completely packed in cartons and ready for shipment.
FOR WHOM THIS FRI?
- Retailers
- Importers
- Wholesalers
- Brand owners
- Buying office
- Trading company
- E-com
- Exporters
- Manufactures
BENEFITS:
- FRI provides the information on Product Quantity and Quality.
- It helps to know the product’s Compliance with the specifications (PO, Style, Measurements, Labelling & Markings, Functionality , safety, and regulatory requirements etc)
- It helps to know nature and percentage of defects in the shipment.
- Refuse defective shipment.
- Facilitate rework easily at manufacturing facility (If required).
- Avoid unexpected costs and delays.
- Avoid last minute surprises in shipment & helps to take correction where necessary in timely manner
- Avoid unexpected costs and delays.
- Save time and secure your business.
- Avoid/minimize business risks like costly recalls / corrections in the destination/ Import Country.
- Maintain the positive Brand value and integrity
- This helps keep monitoring on the factory’s quality level.
- Step 1– Communication of Requirements: The client provides all required Products – Specifications, dimensions, Labelling, packaging, Approved Samples, etc to compare & check against the actual Shipment. The more detailed/precise the information, the more efficient the inspection would be.
- Step 2- Protocol preparation: A pre-filled checklist is prepared with all the client requirements. The checklist will avoid any missing information by the client or the inspector. Also, it enhances the efficiency of the inspector to conduct an organized inspection.
- Step 3– Quality Inspector Planning to factory: After checking with the factory about the 100% goods readiness, Quality Inspector will make necessary travel arrangements to reach the factory Location.
- Step 4- Quantity verification: All physical cartons against packing lists are counted, to check the availability of the whole quantity. Then the Inspector randomly selects a few cartons from all areas as per the sampling plan, opens them & checks their content.
- Step 5- Random selection of samples from Carton: Among the selected cartons, samples are selected randomly by following standard statistical rules to ensure valid findings.
- Step 6- Workmanship Check & Conformity Checks: The drawn samples from the Cartons are checked thoroughly for any defective material, workmanship, packaging, etc against the provided specifications & approved Samples. The defects should be within the Acceptable Quality Level (AQL). If not, the Inspection is failed.
- Step 7- Testing in the Factory: The Inspector performs some tests that are specific to the Product, with the factory’s equipment. These tests can vary according to the Products. For example – Checking the fabric weight, Drop test on export cartons, etc.
- Step 8- Inspection Report Preparation: After completion of checking all required Pieces as per the Sampling plan thoroughly, the Inspector issues a report that describes the actual findings demonstrated with evident pictures. The report documents the findings with actual quantity, visual defects, conformity to requirements, packaging & on-site test.
- Step 9- Shipment Release Authorisation: Report will be sent to the client via email within 24 working hrs after the completion of Inspection. And the final decision on acceptance or rejection of shipment is up to the client.
To know the parameters covered in a Final Random Inspection, please download the report by visiting https://www.rsjqa.com/useful-corner/sample-model-reports
DEFINITION
- Container Loading Inspection is carried out to ensure total quantities of products are loaded securely and safely without any damage.
- This inspection is to verify that packed goods meet your specifications and requirements including:
- Product Types
- Quantity
- Labelling
- Shipping Marks
- Packing & Packaging
- This inspection is to guarantee that packed goods are securely loaded for shipment.
ASPECTS CHECKED IN CONTAINER LOADING INSPECTION:
- BEFORE LOADING:
- Loading information
- Specification/ Shipment/ Packing
- Conformity of product
- 7 Point check of container
- DURING LOADING:
- Safe handling
- Right sequence
- Proper placement
- AFTER LOADING:
- Proper securing of goods
- Container seal
- To know the parameters covered in a Container Loading Inspection, please refer a model report by visiting https://www.rsjqa.com/useful-corner/sample-model-reports
EXECUTION OF CONTAINER LOADING INSPECTION:
- STEP 1: Order booking
- STEP 2: Co- ordination with Factory/Supplier
- STEP 3: Order confirmation
- STEP 4: Conduct inspection
- STEP 5: Send report to client.
BENEFITS
- Ensure whole production is shipped.
- Verify the correct quantity has been loaded.
- Get goods loaded with care.
- Know the condition of containers.
- It helps to know:
- Total quantity of goods packed.
- What exactly is loaded in the container.
- Loading/unloading process for minimize breakage and maximize space utilization.
- Package/packaging method.
- Condition of container and its details.
WHERE IT TAKES PLACE:
Container Loading Inspection will take place right in front of the vendor/ factory/ manufacturer/ forwarding party premise while loading the goods inside the container.
The During Product Inspection is a popular quality assurance measure. It enables businesses to check the quality of their semi-manufactured products and gives them better scope for correction.
DUPRO is beneficial to manufacturers. That’s why many businesses have included it in their manufacturing process.
If you’re unsure about its utility, the following points will help you in removing your confusion:
- Better Quality Control
- In any manufacturing process, some defective pieces get manufactured in a batch. It could be because of a technical error or some other reason.
- DUPRO is done when the product is at 40%-50% of its manufacturing process. The products are inspected thoroughly. They get inspected for any faults or errors, and it is made sure that the faulty products are sent back for correction. You get more control over the quality of your products, and you no longer must rely on any chances.
- Reduction in Losses
- When customers receive defective pieces, they return them to the retailer. You don’t make a profit on returned items. Quality inspection measures like DUPRO ensure that you avoid this from happening.
- By conducting During Production Inspection, you will be ensuring that you correct every faulty product present in your manufactured batches.
- It will enable you to check on the quality of products throughout the production and reduce the chances of the release of faulty products.
To review more information about During Production Inspection, Please visit https://www.rsjqa.com/useful-corner/sample-model-reports to get a model report.
- Enhanced Brand Reputation
- When you inspect every product you manufacture, you ensure that you only produce perfect products. This means you don’t release defective pieces.
- It helps in retaining all the existing customers as they will be happy on your product quality. Also, it attracts more new customers. A better reputation leads to more sales and easier marketing.
INTRODUCTION:
- It is very essential to know that you are sourcing from a manufacturing site that employs better quality systems and good manufacturing processes. The Factory Evaluation ensures the selection of appropriate supplier and their understanding of customer’s quality requirements and meeting the specifications.
- Evaluating a current or potential supplier with Factory Evaluation services will provide you & know about the detailed information on Manufacturer of your Product.
WHAT IS FACTORY AUDIT?
- It is a systematic analysis conducted by an expert at the supplier’s facility to assess the supplier’s quality assurance system, capacity, and their capability to meet various requirements of the buyer. The auditor examines manufacturing processes, process controls & supplier control systems to make an honest appraisal of their potential.
- The scope of the audits is very wide. In broad terms we can categorize it as follows:-
- Factory Audit (Technical)
- Social Audit
Aspects considered during technical audits:
- Machineries
- Facilities
- Equipment
- Manpower (Recruitment and Training)
- Manufacturing Process
- An Assessment of Internal Quality Management System
- House Keeping
- Major Markets & Products
IMPORTANCE:
- Performing a technical Audit is a cost-effective, time-efficient way to compile a complete profile of your supplier, so that you know if they’re able to reliably deliver before you give them business
- Ensure the existence of target set up
- Evaluate the capacity and capability
- Verify their strength/capability in manufacturing targeted product lines.
- Evaluate the existing quality management system.
- Verify whether they are already into manufacturing.
- Finalize potential factory to place an order along with few backups for future.
- Ensure the new or existing manufacturer can deliver quality products, undertake continuous improvements, and operate efficiently.
- By providing a means to examine a factory’s structure, organization, quality process and experience, the audit enables you to compare potential suppliers and select a viable source.
BENEFITS:
- With systematic evaluation of supplier, the customer will have the following benefits.
- Get a snapshot of supplier practices and organization and implement corrective actions plans wherever required.
- Evaluate risks of non-quality and determine adapted quality control measures.
- Establish mutual beneficial partnerships with a pool of suppliers.
- Avoid chances of selection of a technically non-competitive supplier.
- Save time and money – by improving the efficiency and productivity of your vendors and suppliers through process improvement as well as reduced rework and repair.
WHO IS IT FOR?
- This is required for a customer who sources or imports merchandise from a new supplier or increasing business volume/ product range from existing supplier.
The objective of conducting a factory audit is to confirm that the factory can deliver the right product at the right timing. Regular audits of a given factory can also encourage progress over time by pointing to areas of Improvement.
The following are the steps involved in the Factory Audit conduct.
- Step 1 – Factory Audit proposal on selected Supplier from Potentials: A Factory audit usually takes place after a group of potential Supplier has been screened down to fewer better Supplier. Factory audit is the expensive & most in-depth form of Supplier evaluation.
- Step 2 – Objective: The Main Objective of the Factory audit is to find out one best Supplier & a few others to keep as a backup.
- Step 3 – Documents Verification: The Auditor asks & verifies all financial documents of the factory, adding to this the auditor will be verifying factory official licenses & certifications, also looks for the other customer orders.
- Step 4 – Observation of the Production Area: The auditor will check & describe the main types of products seen on the production line, and the Production organization such as Facilities, equipment, workers, and product flows. The below are the key questions to answer.
- Is the factory Capable of producing the Buyer’s Products?
- Does this factory focus on cost management, and if it could handle complex workmanship?
- What is the approximate Capacity ( in the number of Pieces/month) for the buyer’s Product?
- Step 5 – Verification of the Quality System: The auditor follows the checklist based on the ISO9000 series & verifies the incoming material, in-process products & finished goods. The main objective of this verification is to find out if there are any issues with the factory’s quality System and to evaluate their reliability.
- Step 6 – Social Compliance: The auditor checks on the factory to see if all the Country regulations, Criteria of SA8000 & ISO9001 are being met & followed. In this section, the auditor will verify pay records, worker interviews, observations in the workshop, etc. Commonly, Social compliance audit is conducted separately as an individual audit. The main objective is to avoid public relations risks for the Importer or the retailer.
- Step 7 – Report Preparation: After all the gatherings of Information from the factory, the auditor prepares his report based on the actual observations & Subjective evaluation. Then type the report, illustrate with the required Photos, and send it to the customer for their Review. Then by reviewing the Report, the customer will be deciding whether to approve that factory to place the order.